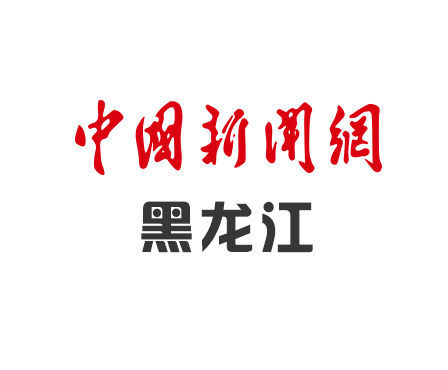
中新网黑龙江新闻12月28日电(谢文艳)28日,在大庆石化乙烯二部苯乙烯联合车间脱氢单元装置区,黄斌正在同技术人员讨论下一步提质增攻关方向。他们刚刚成功实践的“金点子”,节约工业水补水量2.6万余吨,节约费用85万余元,工业废水变废为宝,提质增效显著。
大庆石化鼓励员工打破思想的牢笼,坚定“一切成本皆可降”信心,保持创新精神,加强与行业内的对标,学习吸收先进技术,遇到难题时,多取经,找规律,克难关,落实“金点子”,提质增效。
苯乙烯联合车间脱氢单元,在生产过程中,使用1.0兆帕蒸汽和乙苯混合后,进入脱氢反应器,发生脱氢反应,蒸汽为反应提供热量,最终冷凝形成工艺凝结水,经过沉降分离后,外送至公用工程二部污水装置区,外送工艺凝液量每小时23吨,形成浪费。
针对外送工艺凝液量大的实际,乙烯二部苯乙烯联合车间主任、攻关小组组长黄斌,带领管理技术人员,与同行业苯乙烯装置展开对标,展开多项讨论,发现同行大多都顺利实现了回收使用,这让黄斌他们坚定了信心:人家能做到,我们的装置肯定同样具备回用工艺凝液的潜力。
黄斌他们明白,要想实现提质增效,必须把装置每小时产生的23吨工艺凝液利用起来,但是该怎么做呢?通过与3家完成工艺凝液回收利用的苯乙烯装置对标后,发现他们的共同之处,是将处理完的工艺凝液,作为装置用水使用。
于是,在确认了本装置工艺凝液质量符合生产要求,并经过反复技术论证后,黄斌带领技术人员选择了最为经济实惠的方案,即将工艺凝液引为工业水,替代日常生产使用的一部分工业水量。
有多经济实惠呢?只需在现场增设一根10米左右的管线,以及几个阀门即可完成改造,而这些配件,大多是车间利旧而来,成本消耗极低。
黄斌说:“为了节约费用,我们利用装置现有的碳保护床和循环回水总线,以最短流程,将装置的工艺凝液外送至公用工程二部的供水联合车间,这样一来,不仅降低了外排工业污水的总量,同时也减少了工业水的补充量,一举两得。”
改造完成投用后,装置每小时自产的23吨工艺凝液,约有13吨会以工业水的新身份
重新回到流程中。这一招“自产自用”,不仅大幅减少送往公用工程二部的水量,还降低了装置外引的工业水量,自9月份运行至今,3个月便为企业省下85万余元的费用,节能减排、降本增效显著。
(完)